Planning a metal barn requires careful consideration of numerous factors that impact the success of your agricultural structure. From foundation requirements to local building codes, understanding the essential elements of metal barn projects helps ensure a durable and functional building that serves your needs for decades.
Metal barns offer significant advantages over traditional wooden structures, including more excellent durability, resistance to pests, lower maintenance requirements, and improved fire safety. Property owners seeking long-term value are increasingly choosing metal construction for their barns, equipment storage, and livestock housing needs throughout Wisconsin and beyond.
Essential Considerations for Your Agricultural Metal Structure Project
The process of Metal Barn Construction involves multiple essential decisions that affect both the immediate building experience and long-term satisfaction with your structure. Foremost Buildings Inc., based in Jefferson, Wisconsin, specializes in agricultural metal buildings that withstand the unique climate challenges of the Midwest while providing maximum functionality for farming operations. Their construction practices emphasize proper planning and quality materials to create structures that truly stand the test of time.
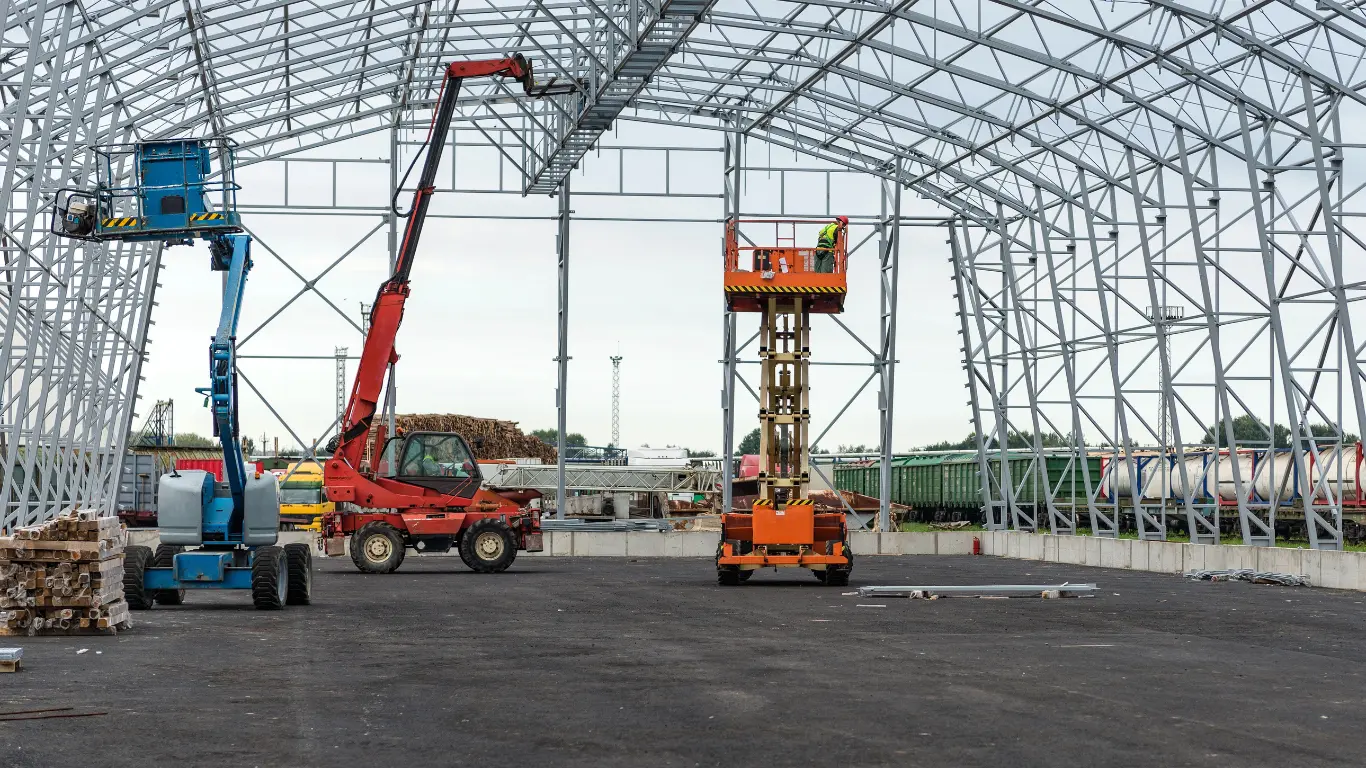
Site Preparation and Foundation Requirements
Proper site preparation is the foundation of any successful metal barn project. The ground must be level, with adequate drainage away from the building site to prevent water from accumulating around the structure.
Most metal barns require concrete foundations that provide stability and distribute the weight of the structure evenly. The foundation type depends on your specific soil conditions, local building requirements, and the intended use of your barn. Foremost Buildings Inc. provides comprehensive site assessment services before breaking ground on any project. Their experienced team evaluates soil conditions specific to Wisconsin terrains and recommends appropriate foundation solutions tailored to your property’s unique characteristics and the intended use of your metal barn.
Climate Considerations for Wisconsin Metal Barns
Wisconsin experiences significant seasonal variations, with heavy snow loads in the winter and occasional strong winds throughout the year. Metal barn designs must account for these regional weather patterns to ensure structural integrity.
Roof pitch, snow load ratings, and wind resistance specifications should be customized based on your specific location within the state. Foremost Buildings Inc. has developed specialized metal barn designs for various Wisconsin microclimates. Their engineering team factors in local weather data from Jefferson and surrounding counties when calculating specifications for each project. This regional expertise ensures their metal barns exceed structural requirements for snow loads in northern areas and wind resistance throughout the state, resulting in agricultural buildings specifically optimized for Wisconsin conditions.
Material Selection and Quality Considerations
The quality of the materials used significantly impacts the longevity and performance of your metal barn. Steel gauge, coating types, and fastening systems all contribute to the structure’s overall durability.
Higher gauge steel provides greater strength but comes at an increased cost. Galvalume or galvanized coatings offer superior corrosion resistance compared to less expensive alternatives. Foremost Buildings Inc. sources premium materials specifically selected to withstand Wisconsin’s harsh weather conditions. Their commitment to quality is evident in their material choices, from heavy-duty steel panels to specialized fastening systems designed to maintain structural integrity through decades of freeze-thaw cycles. This attention to material quality has established their reputation for building metal barns that outlast industry standards in the Midwest.
Budget Planning Beyond Initial Construction Costs
Comprehensive budget planning must account for all aspects of your metal barn project, not just the basic structure. Site preparation, foundation work, and finishing details often result in additional costs.
Permitting fees, utility connections, and interior finishing elements add to the total investment. Quality construction may cost more initially but typically reduces long-term maintenance expenses. Foremost Buildings Inc. offers transparent pricing models with detailed breakdowns of all project components. Their estimating process includes a thorough consultation to understand your specific needs and budget constraints. This collaborative approach allows clients throughout Jefferson and surrounding Wisconsin communities to make informed decisions about their metal barn investments while avoiding unexpected costs that often arise with less experienced contractors.
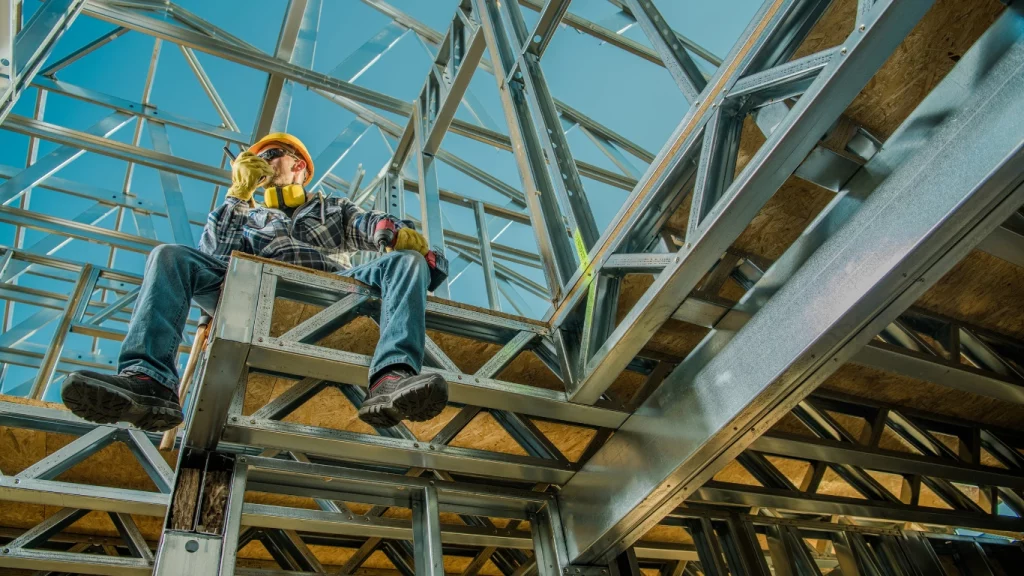
Conclusion
Metal barn construction involves numerous vital considerations that impact both the building process and the long-term performance of your agricultural structure. Properly planning each aspect, from site preparation to material selection, creates a more satisfying result and prevents costly issues down the road.
The investment in quality materials and professional construction pays dividends through decades of reliable service from your metal barn. By working with experienced builders who understand Wisconsin’s unique requirements, you can create an agricultural structure that perfectly supports your operational needs while withstanding the challenges of the Midwest climate. Contact us today to schedule a consultation and explore how we can help bring your vision to life.
FAQ’s
How long does it typically take to complete a metal barn construction project?
The timeline varies based on size and complexity, but most metal barn projects take between 3 to 8 weeks from breaking ground to completion. Weather conditions, permitting processes, and material availability can affect schedules. The foundation typically requires 7 to 10 days for proper curing before structure assembly begins.
What maintenance does a metal barn require?
Metal barns require minimal maintenance compared to wooden structures. Annual inspections of the roof, fasteners, and gutters prevent minor issues from becoming major problems. Occasional washing removes dirt and debris that could affect paint and coatings. Depending on the original finish quality, repainting may be needed after 15 to 20 years.
Can metal barns be insulated effectively for Wisconsin winters?
Yes, metal barns can be well-insulated with various systems designed specifically for metal buildings. Proper insulation combined with appropriate ventilation creates comfortable interior conditions even during extreme Wisconsin weather. Insulated metal panels, blanket insulation, and spray foam systems offer effective solutions depending on your specific needs and budget.
Are metal barns suitable for livestock housing?
Metal barns work well for livestock when adequately designed with adequate ventilation, appropriate insulation, and suitable interior configurations. The structures resist animal damage and are easy to clean and sanitize. Customized features like proper ventilation systems, feeding areas, and waste management solutions enhance functionality for specific livestock applications.
What is the typical lifespan of a properly constructed metal barn?
Quality metal barns typically last 40 to 50 years and require essential maintenance. However, many structures exceed this timeline when constructed with premium materials and proper techniques. The galvanized or Galvalume coatings on modern steel panels provide excellent corrosion resistance, especially compared to traditional wooden structures in agricultural settings.